If you’re new to the Mine Safety and Health Administration’s (MSHA’s) Part 46 surface miner training requirements or just looking for some helpful resources, you’re in luck! This guide is intended to offer important information to help mine operators and independent contractors develop a compliant Part 46 Training Plan for surface non-metal, non-coal mining operations.
So, what’s covered in this MSHA Part 46 Training Plan Guide? In this guide, we’ll cover the following:
- Resources for Developing Your Training Plan
- What an “Approved” Training Plan Is
- Contents of an Approved Training Plan
- Definitions of Key Terms and Roles
- Training Plan vs Training Programs
- Templates and Sample Formats
- Additional Rules and Requirements
So, if you need details and insights on how to create and maintain a compliant Part 46 Training Plan, read on! In this guide we’ll walk you through each step in the process of developing your Training Plan, one of the most important documents required by MSHA. Essentially, when an MSHA inspector comes knocking to check on your training documentation, they’ll ask for two main things – 1) your compliant Training Plan, and 2) all your Records of Training. Both of these sets of documents need to be formatted to contain the information MSHA requires. And when it comes to a government inspection of any kind, nobody wants any unpleasant surprises. So, let’s make sure you’ve got everything you need to stay compliant.
1 – Resources for Developing Your Training Plan
For Part 46, MSHA requires that mine operators and independent (mining) contractors develop a training plan that’s:
- Written and formatted with required information,
- Communicated to miners and miners’ representatives within certain timeframes, and
- Properly updated and maintained as needed.
There are several resources to help you define what a compliant training plan is and how to properly format the document. Here are a few options.
MSHA Part 46 Regulations – It’s always wise to start at the source. Before developing your training plan, start by reviewing Title 30 Code of Federal Regulations (CFR) Part 46.3 – Training Plans. That’s the section of Part 46 that provides the core requirements for the contents, timing of communication, and appeal process of your training plan.
MSHA Resources – MSHA also provides training plan guides and tools you may find helpful:
- MSHA Training Plan Guide
- MSHA Part 46 Training Plan Starter Kit
- MSHA Part 46 Online Plan Advisor
You’ll find a links to these and other helpful info on our RESOURCES page.
Call MSHA – You can call MSHA for assistance at 877-778-6055.
Contact Us – And you can always reach out to us for guidance as well. Just send us a message via our Contact Us page and we’ll get right back to you!
2 – What an “Approved” Training Plan Is
While MSHA requires that Part 48 Underground Miner Training Plans are submitted to them for approval, this is not the case for Part 46 Surface Miner Training Plans. For Part 46, MSHA allows mine operators and mining contractors to develop a plan that meets stated requirements without having to submit the document to MSHA for official approval.
In Part 46.3 (b), MSHA states that “A training plan is considered approved by us if it contains, at a minimum, the following information:” We’ll cover the details of the training plan contents in the next section. But this effectively means that you can develop your own written training plan as long as it has the required info.
So for Part 46, “considered approved” actually means that MSHA is making you responsible for creating a document that meets the minimum informational requirements they lay out. But even though they don’t need to see it in advance, they may ask to review it during an inspection. So, it’s wise to do it right the first time.
However, if you choose to develop a plan that doesn’t contain the minimum information (which I can’t think of a good reason why you’d do that…), MSHA does require you to submit it for approval.
3 – Contents of an Approved Training Plan
An MSHA Part 46 training plan is considered approved if it contains, at a minimum, the following five sets of information:
- Mine or Contractor Details – “The name of the production-operator or independent contractor, mine name(s), and MSHA mine identification number(s) or independent contractor identification number(s);
- Responsible Person – The name and position of the person designated by you [the mine operator or mining contractor] who is responsible for the health and safety training at the mine.
- Teaching Methods, Subjects, and Times – A general description of the teaching methods and the course materials that are to be used in the training program, including the subject areas to be covered and the approximate time or range of time to be spent on each subject area.
- Competent Person(s) – A list of the persons and… who will provide the training, and the subject areas in which each person and/or organization is competent to instruct; and
- Evaluation Procedures – The evaluation procedures used to determine the effectiveness of training.”
MSHA doesn’t specify exactly how this information must be formatted but they do offer a template that many companies use.
4 – Definitions of Key Terms and Roles
MSHA uses several terms that have very specific meanings related to creating and maintaining compliant written documents. Here are MSHA’s definitions and interpretations of key terms for each of the five sets of required training plan information.
- Mine or Contractor Details
- Name of the production-operator or independent contractor – “Operator means any production-operator, or any independent contractor whose employees perform services at a mine.” This is typically the name of the mining company or contractor company.
- Mine name(s) – This should be the site name, number, or location for either a mine or contractor company. The mine name helps identify the specific location that the training plan will be in effect for, since many mine operators my have multiple mine sites and associated mine names.
- MSHA mine identification number(s) or independent contractor identification number(s) – An MSHA Mine ID is a unique identifying number required for each U.S. underground and surface mine site before any operations may begin. Independent contractors performing services or engaged in construction work at a mine may also apply for an MSHA Contractor ID online for free.
- Responsible Person
- This must be the name of a person and their title, not a company name, designated by the mine operator or mining contractor who is responsible for the health and safety training at the mine.
- This person may be the production-operator or independent contractor.
- It’s also common for a safety manager to be the responsible person. Since that person may also be experienced in required training subjects, that individual could also be designated as a competent person to deliver training.
- Teaching Methods, Subjects, and Times
- Teaching methods – These are the methods used by the competent person to effectively train miners and mining contractors on the required subjects. These methods may include:
- Lecture
- Discussion
- Audio-visual media
- Tour of a facility or site
- Computer-based or online training
- Course materials – These are the types and sources of training materials to be used by the competent person to deliver training. Course materials may include:
- MSHA documents or regulations
- Company policies
- Vendor or manufacturer information
- Other applicable laws and regulations
- Subject areas to be covered – These are the required subjects, at a minimum, per training program that must be listed. MSHA outlines required subjects for each of the following training programs:
- New Miner
- Newly Hired Experienced Miner
- New Task
- Site-Specific Hazards
- Annual Refresher
- Approximate time or range of time to be spent on each subject area – MSHA allows for planned training time to be displayed as a range. There’s no specific requirement about what that range must be. Here are some examples of how you could list the approx. time per subject:
- 30 minutes to 1 hour
- 1 to 2 hours
- 30 minutes to 1.5 hours
- Teaching methods – These are the methods used by the competent person to effectively train miners and mining contractors on the required subjects. These methods may include:
- Competent Person(s)
- Competent Person(s) – MSHA defines a competent person as “a person designated by the production-operator or independent contractor who has the ability, training, knowledge, or experience to provide training to miners in his or her area of expertise. The competent person must be able both to effectively communicate the training subject to miners and to evaluate whether the training given to miners is effective.” This is the person or persons who will actually provide the training.
- Subjects – You must also list the subject areas in which each person is designated competent to instruct. Again, MSHA outlines the minimum training subjects per training program in Part 46. We’ll cover those in more detail in a later section of this article.
- Evaluation Procedures
- While MSHA doesn’t require that specific evaluation procedures are used, they allow you to select the best method for determining the effectiveness of training. Some examples of evaluation procedures include:
- Written or oral tests
- Discussion
- Task demonstration
- On-the-job observation
- While MSHA doesn’t require that specific evaluation procedures are used, they allow you to select the best method for determining the effectiveness of training. Some examples of evaluation procedures include:
5 – Training Plan vs Training Programs
In case there’s any confusion about MSHA’s use of the terms “training plan” and “training program,” here’s some clarification.
A training plan is the document that contains effective programs for training miners based on the requirements outlined in Parts 46.5-46.8 and Part 46.11.
A training program is the specific set of required subjects, amounts of training time, and completion deadlines associated with specific roles or training types.
Within your training plan, you’ll need to specifically outline each of these training programs. Here’s how MSHA defines and outlines the training programs:
- New Miner – “a person who is beginning employment as a miner with a production-operator or independent contractor and who is not an experienced miner.”
- Minimum of 24 hours of training.
- 4 of the 24 total hours must be completed prior to the new miner beginning work at the mine. Those 4 hours must include at a minimum, these topics:
- Introduction to the mine site
- Hazard recognition and avoidance
- Emergency procedures
- Health and safety aspects of tasks
- Statutory rights of miners and miners’ representatives
- Line of authority
- Hazard reporting
- Training that must be completed within 60 days of a miner beginning work at the mine must include (with no minimum training time amount):
- Respiratory devices
- First aid
- Any remaining balance of the 24-hour training requirement must be provided within 90 days of the miner beginning work at a mine.

- Newly Hired Experienced Miner – “an
experienced miner who is beginning employment with a production-operator or
independent contractor.”
- No minimum training time requirements.
- All of the same 7 training subjects as required for New Miners must be completed prior to the miner beginning work at the mine.
- Training that must be completed within 60 days
of a miner beginning work at the mine must include (with no minimum training
time amount):
- Respiratory devices
- No minimum training time requirements.
- New Task – “a new task in which [the
miner or mining contractor] has no previous work experience with training in
the health and safety aspects of the task to be assigned, including the safe
work procedures of such task, information about the physical and health hazards
of chemicals in the miner’s work area, the protective measures a miner can take
against these hazards, and the contents of the mine’s HazCom program.”
- No minimum time requirement.
- Training must be provided when a miner is assigned a new task or when changes at the mine occur that affect the mine’s health and safety.
- Training must be provided BEFORE the miner performs the new task.
- Site-Specific Hazards – “Site-specific
hazard awareness training is information or instructions on the hazards a
person could be exposed to while at the mine, as well as applicable emergency
procedures. The training must address site-specific health and safety risks,
such as unique geologic or environmental conditions, recognition and avoidance
of hazards such as electrical and powered-haulage hazards, traffic patterns and
control, and restricted areas; and warning and evacuation signals, evacuation
and emergency procedures, or other special safety procedures.”
- No minimum time requirement.
- Site-specific hazard training must be provided BEFORE any person is exposed to mine hazards.
- Must be provided to any person who is not a
miner but is present at the mine, including:
- Office or staff personnel
- Scientific workers
- Delivery workers
- Customers
- Maintenance or service workers
- Vendors
- Visitors
- Not required for any person accompanied at all times by an experienced miner familiar with the mine site.
- Annual Refresher – This is 8 hours of training that must be provided no later than 12 months after a miner either begins work or has completed a prior annual refresher training. While MSHA suggests many potential training subjects, the only required annual refresher subject is referred to as “changes at the mine that could adversely affect the miner’s health or safety.”
- Minimum 8-hour time requirement.
- Training must be provided no later than 12 months after:
- Miner begins work at the mine, or
- Miner’s last annual refresher training
- Must include “changes at the mine.”
- May include:
- Mandatory health and safety standards
- Information about the physical and health hazards of chemicals in the miner’s work area
- The protective measures a miner can take against these hazards
- The contents of the mine’s HazCom program
- Transportation controls and communication systems
- Escape and emergency evacuation plans
- Firewarning and firefighting
- Ground conditions and control
- Traffic patterns and control
- Working in areas of highwalls
- Water hazards, pits, and spoil banks
- Illumination and night work
- First aid
- Electrical hazards
- Prevention of accidents
- Health
- Explosives
- Respiratory devices
- Equipment Hazards
- Mobile equipment (haulage and service trucks, front-end loaders and tractors)
- Conveyor systems
- Cranes
- Crushers
- Excavators
- Dredges
- Maintenance and repair (use of hand tools and welding equipment)
- Material handling
- Fall prevention and protection
- Working around moving objects (machine guarding)

6 – Templates and Sample Formats
There are several ways to develop a compliant training plan. You can:
- Build your own – Build your plan from scratch
based on the Part 46 training plan requirements.
- Pro – You retain control and access to your files and information.
- Con – Will take extra work to produce.
- MSHA sample – Use an existing MSHA sample
plan and fill it out manually.
- Pro – You retain control and access to your source files and you can work from information provided directly from MSHA.
- Con – Will take extra work to produce.
- MSHA online tool – Use MSHA’s online
Electronic Training Plan Advisor.
- Pro – Very easy to use. Offers all required information fields in a format accepted by MSHA.
- Con – Online access requires MSHA ID for login. You don’t retain control of source files.
MSHA provides a sample training plan template in its 30 CFR Part 46 Starter Kit with Sample Training Plan. Here’s what the New Miner program section of their sample plan looks like.
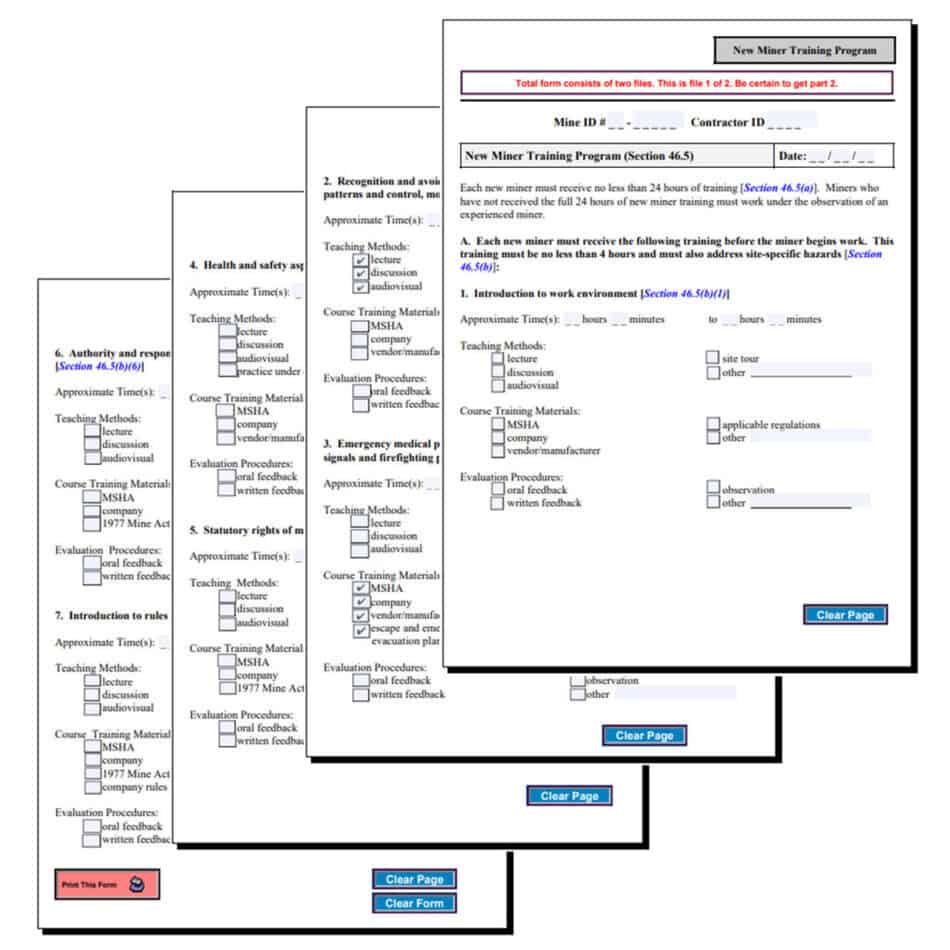
You can print it out and fill it in manually.
You can find a link to this download on our RESOURCES page.
MSHA also provides an Electronic Plan Advisor, a genuinely helpful tool that walks you through the process online and allows you to print the training plan when you’re done. Here’s a sample of what the New Miner training program looks like from this tool.
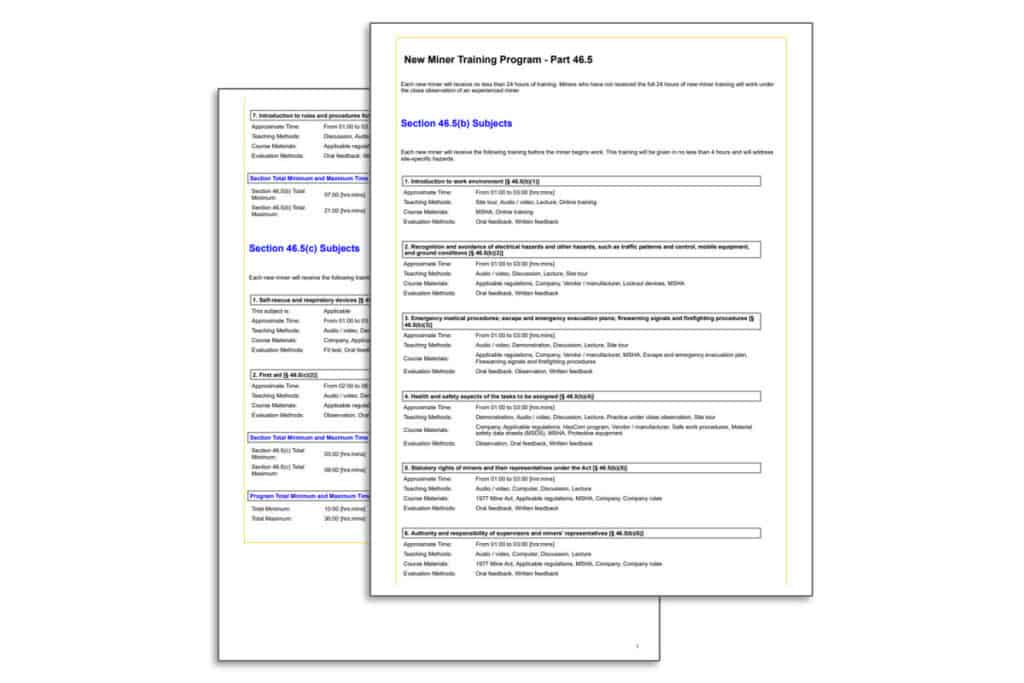
NOTE – You’ll have to be a registered eGov user to log in and you’ll need an MSHA mine ID, contractor ID, or training advisor ID to use this tool. MSHA estimates that it should take 60 to 90 minutes to complete your training plan online.
7 – Additional Rules and Requirements
MSHA makes several requirements for how and when a Training Plan must be displayed, made available, maintained, and generally communicated to mine personnel.
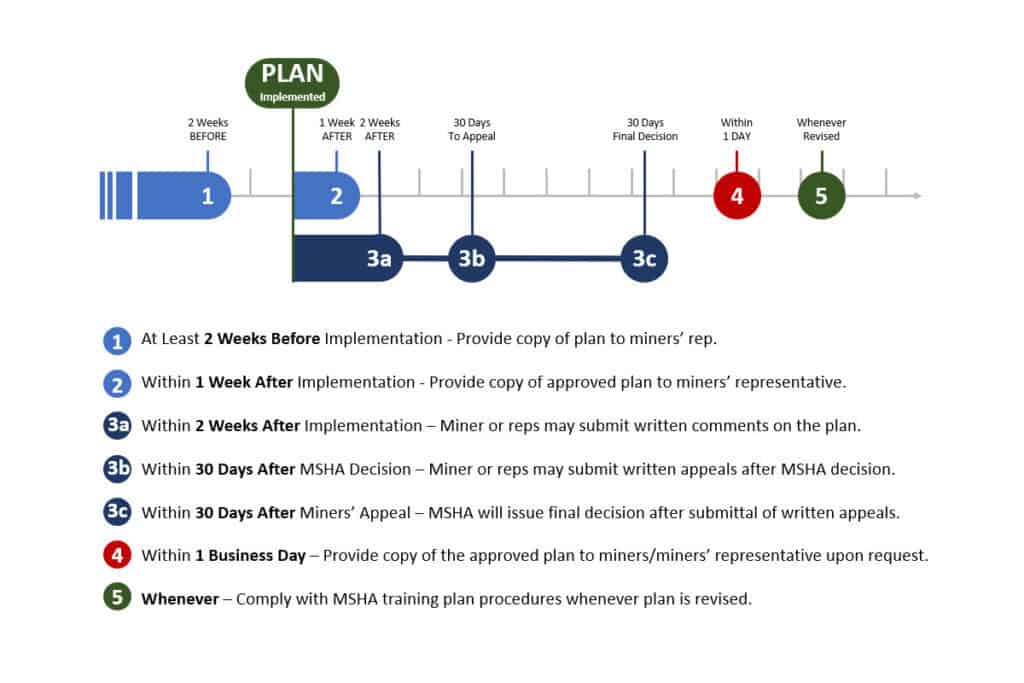
At Least Two Weeks BEFORE– “You must provide the miners’ representative, if any, with a copy of the plan at least 2 weeks before the plan is implemented or, if you request MSHA approval of your plan, at least two weeks before you submit the plan to the Regional Manager for approval. At mines where no miners’ representative has been designated, you must post a copy of the plan at the mine or provide a copy to each miner at least 2 weeks before you implement the plan or submit it to the Regional Manager for approval.”
Within One Week AFTER – “You must provide the miners’ representative, if any, with a copy of the approved plan within one week after approval. At mines where no miners’ representative has been designated, you must post a copy of the plan at the mine or provide a copy to each miner within one week after approval.”
Within Two Weeks AFTER – “Within 2 weeks following the receipt or posting of the training plan under paragraph (d) of this section, miners or their representatives may submit written comments on the plan to you, or to the Regional Manager, as appropriate.”
Within 30 Calendar Days – “If you, miners, or miners’ representatives wish to appeal a decision of the Regional Manager, you must send the appeal, in writing, to the Director for Educational Policy and Development, MSHA, 201 12th Street South, Arlington, VA 22202-5452, within 30 calendar days after notification of the Regional Manager’s decision. The Director will issue a final decision of the Agency within 30 calendar days after receipt of the appeal.”
Within One Business Day – “You must make available at the mine a copy of the current training plan for inspection by us and for examination by miners and their representatives. If the training plan is not maintained at the mine, you must have the capability to provide the plan within one business day upon request by us, miners, or their representatives.”
Whenever – “You must comply with the procedures for plan approval under this section whenever the plan undergoes revisions.”
Related Questions
Which is an MSHA ID?
Check out our article on MSHA IDs – “What Is An MSHA Mine ID And How Do I Get One?”
How do I fill out a 5000-23 Certificate of Training?
Check out our article on the 5000-23 – “How To Fill Out An MSHA 5000-23 Certificate of Training”