Thinking backwards about everyday items can be a great way to start understanding the world around us. Here’s an example – Think about concrete. We see it everywhere. It’s the single most common building material in the entire world. But where does it come from? Well, it’s mostly made up of sand and gravel, which likely came from a surface mine not far away. And that process of surface mining for sand and gravel is what we’ll discuss is some detail in this article.
So, what are the main steps in the surface mining processes? The four main steps in surface mining involve:
- Locating mineral deposits
- Removing overburden
- Extracting material
- Processing the commodity
With a short introduction to how a surface mine gets started, we’ll focus primarily on the actual processes and steps involved in removing and processing materials at a surface mine. Even with a commodity that may seem as simple as sand and gravel, there’s a significant amount of production design, heavy equipment, and machinery that goes into getting different sizes (dimensions) of gravel and crushed stone, as well as a range of types of sand, ready for use in concrete and other products.
We’ll use open pit surface sand and gravel (aggregate) mining as the primary example of the surface mining process, with the understanding that techniques and processes will vary for other minerals, types of stone, and types surface mines.
1 – Locating Mineral Deposits
Often referred to as the “prospecting” stage of mining, this type of dedicated and professional exploration involves detailed geologic surveys and testing. The purpose of prospecting is to assess the economic value of a mineral deposit by identifying and mapping the type, quality, volume, and accessibility of the material to be mined.
When geological information supports the economic viability of mining an area, the process of mine development follows. This includes the design of the pit (extraction zones) and construction of mine roads and processing facilities.
So, prior to any actual mining, the entire mine property is meticulously planned with areas dedicated to mineral extraction, on-site material transport, processing, stockpiling, and finished product distribution.
2 – Removing The Overburden
Once the material deposits have been clearly identified and located, the first step towards exposing and accessing the minerals can begin.
Mineral deposits, such as sand and gravel, may begin at an average depth of about 8 feet (2.5 meters) and continue to as much as 150 feet (45.72 meters) below ground. In order to access the mineral deposit and begin extraction, the surface layer of trees, vegetation, and soil (the overburden) must be removed.
Removing the overburden involves use of heavy equipment to scrape and push the soil and vegetation out of the way. Back hoes, bull dozers (dozers), and scrapers are types of heavy equipment used to remove the surface stone and topsoil covering the mineral to be mined.
Excess overburden material may be used for construction of berms surrounding the mine. Additional equipment may be used to relocate and stockpile overburden material for future mine reclamation efforts when mineral deposits have become depleted.
The reclamation process involves replacing topsoil and replanting indigenous trees and vegetation.
3 – Extracting Material
With the overburden removed and the mineral deposit exposed, extraction can begin. Extraction involves the use of heavy machinery to systematically remove material from the deposit so it can be transported to an onsite processing facility to be prepared for use in a variety of finished products.
Extraction equipment may include:
- Bucket Wheel Excavators – Often massive machines with a large reverse-rotating wheel that operates tangent to the pit wall. The wheel is equipped with multiple buckets that continually scoop and dump material from the deposit as the wheel rotates.
- Draglines – Employ a cable-mounted bucket suspended and operated from a large boom. The bucked is dragged across the pit face to collect minerals and dump the load into a haul truck.
- Front End Loaders – Typically 4-wheeled equipment that scoops material into a wide, front-mounted bucket for loading haul trucks.
- Power Shovels – Track-mounted machines with forward facing buckets to scoop large volumes of material from the pit face and dump into haul trucks.
At a surface sand and gravel mine, for example, a font end loader (loader) is commonly used to scoop large volumes of material from the base of the deposit with its bucket. As material is extracted, a large depression in the earth, the “pit,” develops, exposing more and more of the mineral deposit.
The loader will dump each full bucket into a waiting haul truck or into a hopper or pile that feeds an overland belt conveyor.
- Haul Trucks – Large dump trucks that can range greatly in size and volumes. Haul trucks transport huge volumes of mined material to the processing plant and other areas of the mine as needed. Many haul trucks only operate on specially designed haul roads on the mine property. They are often far too large to be driven on normal civilian roads.
- Overland Belt Conveyors – A type of heavy-duty conveyor that can transport large volumes of mined material and run continuously over long distances. This type of conveyor brings material from the pit to the processing plant. It may also be used to transport processed material from a stockpile to a barge for water transport to a buyer who may use the sand or gravel as a raw material for other products.
Whether using a haul truck or conveyor, the material is transported to either a stockpile area or the first stage of processing at the plant.
4 – Processing Commodity

The processed sand and gravel will ultimately be used as raw materials for products in two key markets – construction and industrial. Mine operators plan and adjust mining processes with customers in these markets in mind.
Processing material at a surface sand and gravel mine is fundamentally a staged filtering process. Raw mined material is brought into the processing plant and systematically screened, washed, and filtered by size from several inches down to fine sand. Here are some of the basic steps involved in processing sand and gravel from a surface mining operation.
Grizzly – As material being transported via haul truck or conveyor from the pit approaches the processing plant, it goes through an initial set of screening bars called a “grizzly,” which prohibits large rocks (cobbles) and boulders that are too big for processing from entering the hopper. The hopper is a large bin that accumulates and releases material onto one or more conveyors for either stockpiling or transport to the next phase in processing.
Scalping Screens – After the grizzly and the hopper, the raw material is sent through the scalping screens, which separate more oversized material from sand and gravel. The remaining material will be washed and sized by additional screens.
These oversized stones excluded from the process may be used at the mine for erosion control or reclamation purposes. They may also be sold for other architectural uses or transported to the crusher as feed material to be reduced into salable crushed stone and sand.
Sizing Screens – After the scalping screens, the material is transported via conveyor into a sizing screen mechanism that can be several stories high. The sand and gravel may pass through several successively smaller vibrating screen decks, each with a high-pressure array of water spray nozzles that wash dirt and debris from the gravel and force sand to the bottom of the sizing screen decks.
At each screen deck, the sized material is separated and transported via conveyor to dedicated stockpiles based on the material size. Stack conveyors then raise sized stone and gravel several stories high to allow for accumulation of massive stockpiles.
Gravel is stockpiled by size ranging from 1/3 inch (8mm) to almost 3 inches (64mm) in width.
Crushing – Larger stones separated at the scalping screen may be diverted by conveyor to a crusher to reduce the stone to specific sizes. Two of the most common types of crushing equipment are jaw and cone crushers.
- Jaw Crusher – This type of crusher may be used as a primary stage in reducing the size of oversized stone. Jaw crushers operate by feeding stone in between two crushing surfaces, a fixed jaw and an angled moving jaw. The opening between the jaws is wider at the point of material entry and narrower at the point of material exit.
- Cone Crusher – This type of crusher feeds stone into a cavity between a stationary housing and an oscillating cone-shaped mechanism that crushes stone to specified dimensions.
Crushed stone is then transported by conveyor to stockpiles based on stone size.
Sand Classifying – The sand washed from the gravel in the sizing screens is pumped to a washing and sizing mechanism called a “classifier.” This is a specialized processing machine that separates the sand from fine silt and further sorts the sand by size and grade. Sand manufactured from the crushing process may also be sent to the classifier.
At mines that produce sand used for specialized construction or industrial purposes, washing is a critical step in the process to ensure that the finished product isn’t contaminated with other material.
Sand is then dewatered and stockpiled by size and quality.
Stockpiling – At the end of each washing, sizing, and classifying process, material is stockpiled. In terms of a surface aggregate mine, this essentially a form of organized storage for your inventory. Large piles of washed sand, gravel, and crushed stone of various sized are created as the output of a variety of processes.
Material can be removed from stockpiles in a couple of different ways, either by loader or by conveyor.
- Loader – Front end loader may scoop material from the edge of a pile to load a truck or supply a collocated cement batch plant.
- Conveyor – Stockpiles may be situated on top of a system of tunnels and conveyors which can load out predetermined amounts of each type and size of material as needed. These conveyors may exit the processing area and transport material in large volumes to a waiting barge or rail car for shipment to a customer.
Angle of Repose – These massive piles may be managed by dozer operators who move and adjust stockpiled material to control the angles of the sides of piles (or slope face) and avoid an unexpected slide or collapse. When piled, granular, unconsolidated material will naturally come to rest at a certain angle – its “angle of repose.” This angle is different for wet and dry material of different sizes and physical properties.
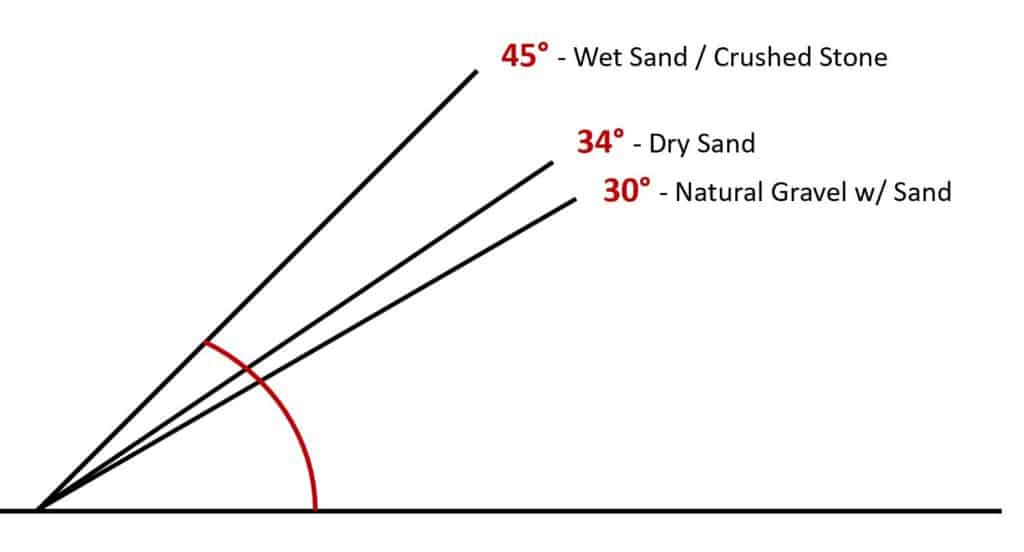
If a material is piled in a way that its slope exceeds its angle of repose, that pile can become unstable and collapse. At a surface mine where tons of material can suddenly shift, slide, or collapse on workers below, it’s extremely important to take measures to avoid this potentially deadly situation.
While several factors can affect the stability of a pile, two activities can create dangers situations if not managed properly:
- Removing material from the base of a pile – Removing material from the base of a pile for use in another area or to load a truck for shipping is a very common activity. However, if the angle of repose isn’t reestablished, the pile may be undercut resulting in a dangerous overhang. Material may be pushed from above to fill in the overhang.
- Adding material to the top of a pile – As material is continually added to the pile from above by the stack conveyor, the slope face of the pile may increase beyond the angle of repose if the pile isn’t managed. A dozer may periodically push material over the sides of the pile to allow it to rest at its angle of repose and regain stability.
Distributing Finished Products
Stockpiles sand, gravel, and crushed stone is directly shipped from the mine to customers in a variety of ways. It can be shipped as separate or mixed raw materials or in the form of concrete for local building projects.
Customers requiring construction or industrial materials may order one specific type and size of material or a mix of several types and sizes of material depending upon the specific use. Mixed materials are ordered with specific percentages of each type of material.
To satisfy customer orders, material can be loaded and shipped by:
- Over-The-Road Trucks – Hauling about 25 tons of material
- Railcars – Shipping about 110 tons of material per car
- Barges – Shipping about 1,500 tons of material per barge
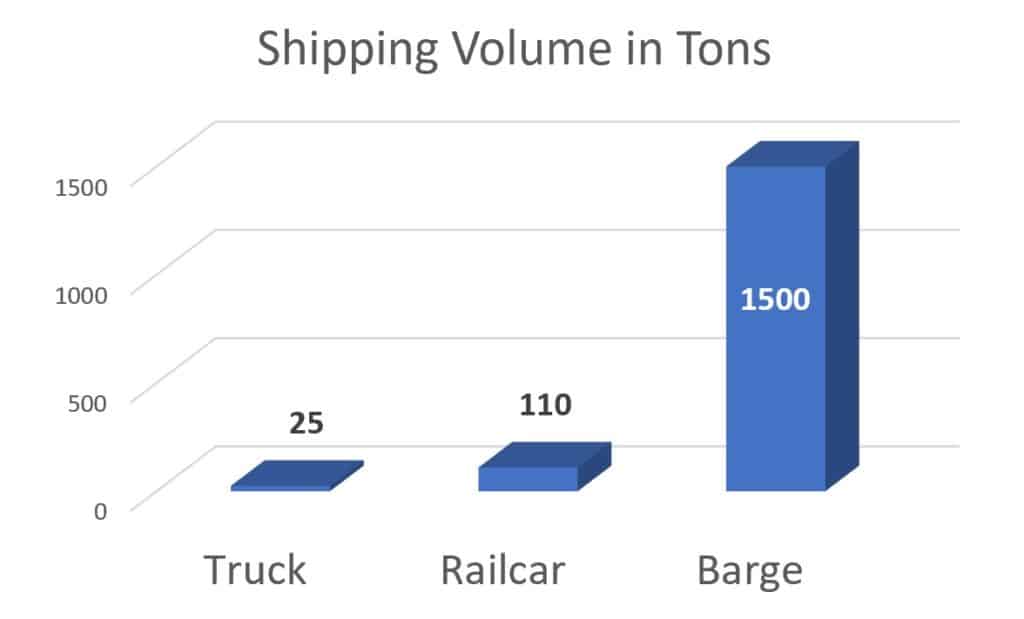
Concrete Production
At many sand and gravel mines, a “batch” or “ready-mix” plant may be collocated on or very near to the mine property. This allows for concrete production to take place on-site, using any formulation of specifically sized gravel with any preferred type of sand based on the use of the finished concrete product.
As part of any building design, the engineering plan will include specific requirement for the strength and hardness of the concrete based on how and where the material will be used in the structure. These requirements equate to a variety of concrete formulas that may be ordered at any time.
The aggregate material is mixed onsite with cement to produce concrete used for virtually any type of local building project. This concrete will be mixed and used the same day. So, production and use of mixed concrete is entirely for local construction.
Since concrete has a very short shelf-life, the production and transport via mixer trucks to waiting customers is very precisely managed to ensure product quality.
Mine Area Reclamation
At large sand and gravel mines, it’s common for areas of deposits to become depleted over time. As the mining areas within the pit shift to follow the deposit, reclamation efforts can begin in areas where active mining has ceased.
Stockpiles overburden can be accessed and moved to refill areas. Trees and other vegetation may be replanted while active mining is taking place in other parts of the mine. This helps mitigate erosion and provides the basis for habitat that can be developing while active mining is still taking place.
Related Questions
What Is The Lifecycle Of A Surface Mine?
- Prospecting, Exploration, and Surveying – Mineral location and mapping of volumes, depth, and quality
- Mine Development – Design and construction of the pit, mine roads, buildings, and processing facilities
- Exploitation – Removal of overburden, extracting, processing, and distributing of mined material
- Reclamation – Ongoing process of replacing topsoil and vegetation as areas of deposits are depleted
- Mine Closure – When all deposits are depleted and the mine has been completely reclaimed
What Are Some Of The Uses Of Sand And Gravel?
Sand and gravel are used for two primary purposes, construction and industrial.
Construction uses include:
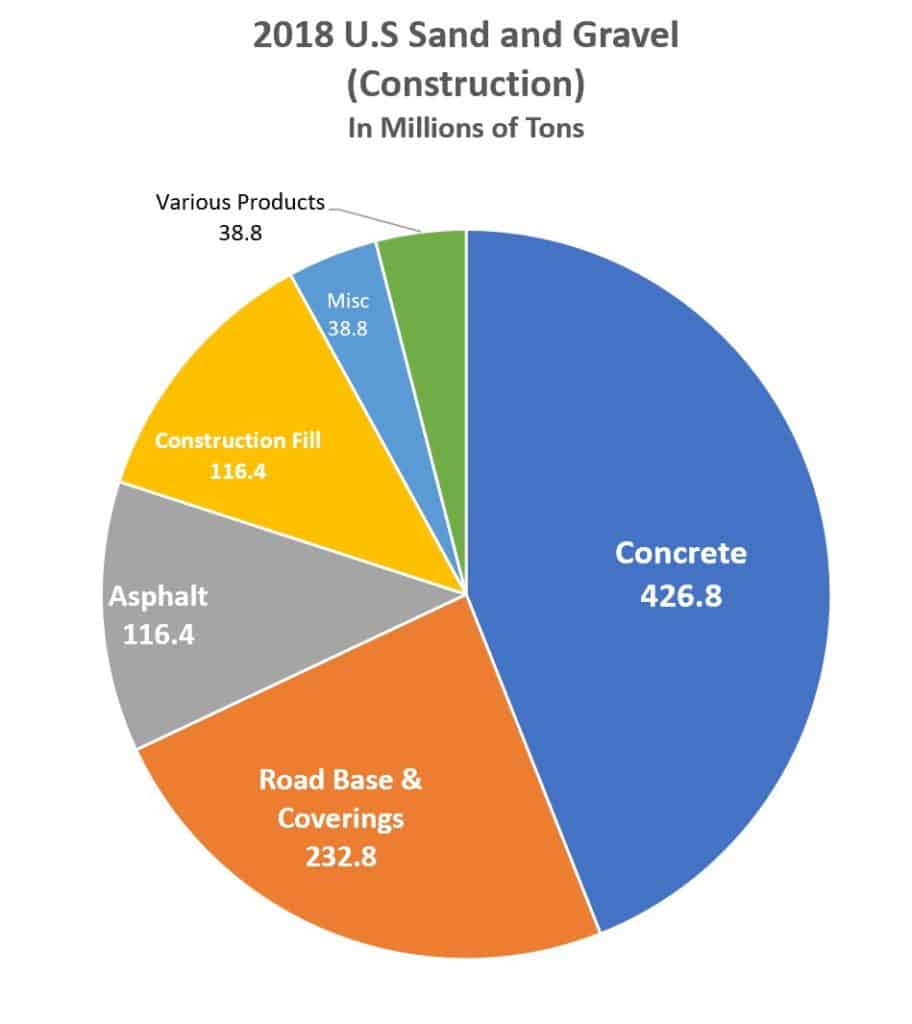
- Concrete for building construction
- Construction materials – concrete blocks, bricks, and culverts
- Masonry products
- Road and Railroad construction materials – asphalt and fill material
- Roofing material
- Building construction foundation fill material
- Traction treatment on slick roads – sand
- Landscaping – a variety of rocks and sand

Industrial uses include:
- Hydraulic-fracturing
- Glass production
- Whole-grain silica
- Specialized filters
- Building products
- Foundry sand
- Ground and unground sand for chemicals
- Recreation sand