The Mine Safety and Health Administration (MSHA) supports, oversees, and enforces safety and training regulations for all U.S. mines. MSHA’s two main training regulations are Part 46 for surface miner training and Part 48 for underground (and surface areas of underground) miner training. Since the vast majority of mines in the U.S. are surface mines, we’ll focus on Part 46 surface miner training requirements in this article.
So, what are MSHA’s Part 46 surface miner training requirements? MSHA’s Part 46 surface miner training requirements include:
- Developing a compliant TRAINING PLAN, including 5 specified training programs
- Delivering compliant TRAINING SUBJECTS by a competent person in specified time frames
- Recording and certifying training by the responsible person on a compliant TRAINING RECORD
If you’re responsible for managing your mine’s training program, or if you’re a contractor about to begin work at a surface mine, the information we’ll cover here just may save you tons of time and effort, and potentially help you avoid costly citations. Our goal is to help you get the information you need to train your team and stay compliant. So, we’ll cover everything in detail and point you toward some valuable resources to help you along the way. And ultimately, this is all about sending miners and mining contractors home safely at the end of the day. There’s a lot to cover! So, let’s get started.
What is MSHA Part 46?
Before we get into the details of Part 46 training requirements, let’s make sure it’s clear what Part 46 actually is.
MSHA Part 46 is one of over 100 “parts” within Title 30: Mineral Resources in the Code of Federal Regulations (CFR), which covers a broad scope of mine safety and training regulations.
Part 46 regulations are for the “training and retraining of miners and other persons at shell dredging, sand, gravel, surface stone, surface clay, colloidal phosphate, and surface limestone mines.”
This means that the Part 46 set of training and documentation requirements cover surface, non-coal, non-metal mines.

TIP! – Check out our article “MSHA Part 46 vs Part 48 – The 3 Major Differences” for more detailed information on these regulations.
Part 46 Overview
While there are many exhausting details involved in getting your team to complete 24 hours of required surface miner training, the entire scope of Part 46 can be reduced to this:
- Create a document
- Do the training
- Create a document

This is what we call the “training sandwich.” The training is the meat (or whatever your sandwich filler preference is) and the documents are the bread. You must have all three to make a sandwich and you must have all three to comply with MSHA’s training requirements.
Let’s expand on that 3-step process.
- Create a document –
- You’ll create a compliant training plan
- that includes MSHA’s 5 training programs.
- New Miner
- Newly Hired Experienced Miner
- New Task
- Annual Refresher
- Site-specific Hazards
- Do the training –
- You’ll have a competent person conduct the training,
- on the required subjects
- in the specified time frames.
- Create a document –
- You’ll create a compliant record of training
- or use an MSHA 5000-23 Certificate of Training form
- to record and certify completed training by signature of the responsible person.
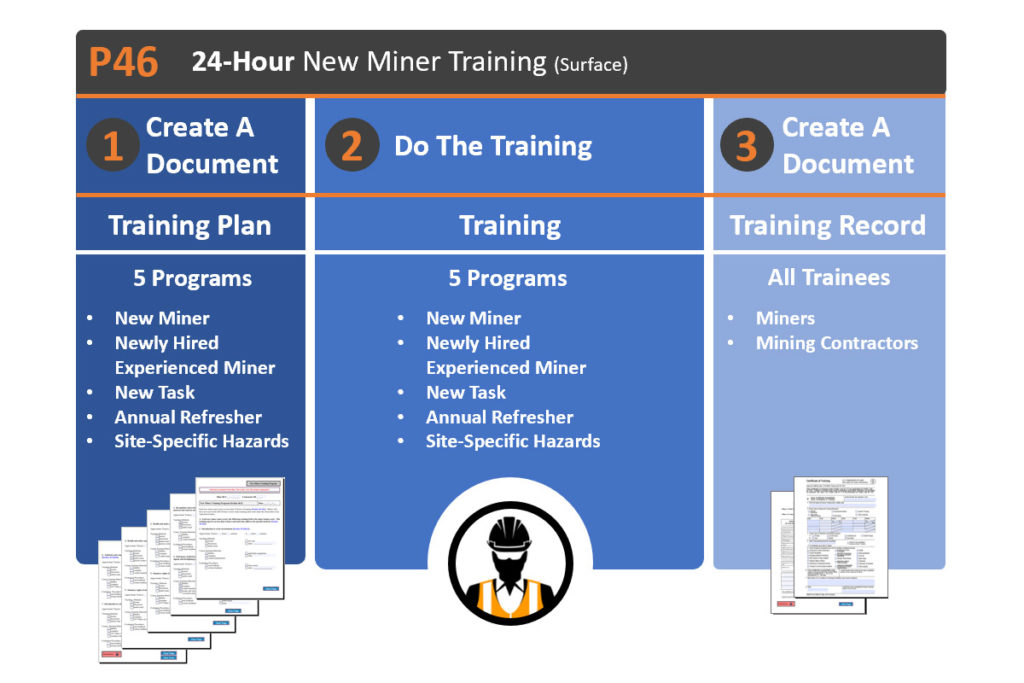
Now, that’s the general idea. Let’s get down to the specifics.
Develop A Compliant Part 46 Training Plan
In Title 30 of the Code of Federal Regulations (CFR) Part 46.3 (a) Training Plans, MSHA states that “You must develop and implement a written plan, approved by us under either paragraph (b) or (c) of this section, that contains effective programs for training new miners and newly hired experienced miners, training miners for new tasks, annual refresher training, and site-specific hazard awareness training.”
The regulations go on to say that “A training plan is considered approved by us if it contains, at a minimum, the following information:”
- Mine or Contractor Details – “The name of the production-operator or independent contractor, mine name(s), and MSHA mine identification number(s) or independent contractor identification number(s);
- Responsible Person – The name and position of the person designated by you [the mine operator or mining contractor] who is responsible for the health and safety training at the mine.
- IMPORTANT – This is the person who will sign your record of training to certify that training has been completed.
- Teaching Methods, Subjects, and Times – A general description of the teaching methods and the course materials that are to be used in the training program, including the subject areas to be covered and the approximate time or range of time to be spent on each subject area.
- Competent Person(s) – A list of the persons… who will provide the training, and the subject areas in which each person and/or organization is competent to instruct; and
- IMPORTANT – This is the person or persons who will conduct training on subjects for which they are deemed competent to teach.
- Evaluation Procedures – The evaluation procedures used to determine the effectiveness of training.”
It’s important to understand that MSHA does not require that you submit your training plan for direct approval from them. That’s why they state that your written plan is “considered approved by us” if you create the document with the required information.
It’s also critical to understand what MSHA means by “responsible person” and “competent person” and how those roles need to be documented in your training plan.
TIP! – Please refer to our article “MSHA Part 46 Training Plan – Essential Development Guide” for:
- Definitions of key terms and roles
- Detailed instructions for developing a compliant training plan
- Requirements for communicating your training plan within your organization
- Additional resources and templates for developing a compliant training plan
Conduct Training On Required Subjects In Specified Time frames
In Parts 46.5-8 and 46.11, MSHA outlines training requirement for each of the 5 training programs that must appear in your written training plan as a guide for conducting your training. We’ll cover each of the 5 training programs in detail, including their:
- Required training subjects
- Specified time frames (where applicable)
- Documentation requirements
In case there’s any confusion about MSHA’s use of the terms “training plan” and “training program,” here’s some clarification.
- A training plan is the document that contains each of the 5 programs for training miners, mining contractors, and mine visitors based on the requirements outlined in Parts 46.5-46.8 and Part 46.11.
- A training program is the specific set of required subjects, amounts of training time, and completion deadlines associated with specific roles or training types. The 5 training programs for Part 46 are:
- New Miner
- Newly Hired Experienced Miner
- New Task
- Annual Refresher
- Site-Specific Hazards
Training must be conducted by a competent person. A competent person is “a person designated by the production-operator or independent contractor who has the ability, training, knowledge, or experience to provide training to miners in his or her area of expertise. The competent person must be able both to effectively communicate the training subject to miners and to evaluate whether the training given to miners is effective.”
TIP! – All competent persons and their associated training subjects must be listed within your training plan.
Training Program Requirements
New Miner Training
Part 46.5 New Miner Training outlines the requirements for training a new miner.
A new miner is defined as “a person who is beginning employment as a miner with a production-operator or independent contractor and who is not an experienced miner.”
The minimum time requirement for new miner training is 24 hours, 4 hours of which (in 7 required subject areas) must be completed before a new miner begins work at a mine. Two subjects much be completed within 60 days of beginning work at the mine. And any remainder of the 24 hours of training must be completed no later than 90 days after a miner begins work at the mine.
TIP! – With consideration to these training deadlines, most mine operators tend to train new miners in 3 consecutive 8-hour days prior to the miner beginning work at the mine. This approach ensures that all new miner training is completed, and all required subjects are covered without having to track training deadlines over several months.
Required training subjects prior to beginning work at the mine with no less than 4 hours of training include:
- Introduction to the work environment, including a mine tour
- Hazard recognition and avoidance
- Emergency procedures
- Health and safety aspects of tasks
- Statutory rights of miners and miners’ representatives
- Line of authority
- Hazard reporting
Required training subjects within 60 days of beginning work at the mine include:
- Self-rescue and respiratory devices (if used at the mine)
- First aid
Required training subjects within 90 days of beginning work at the mine include:
- Any remaining balance of the 24 hours of required training
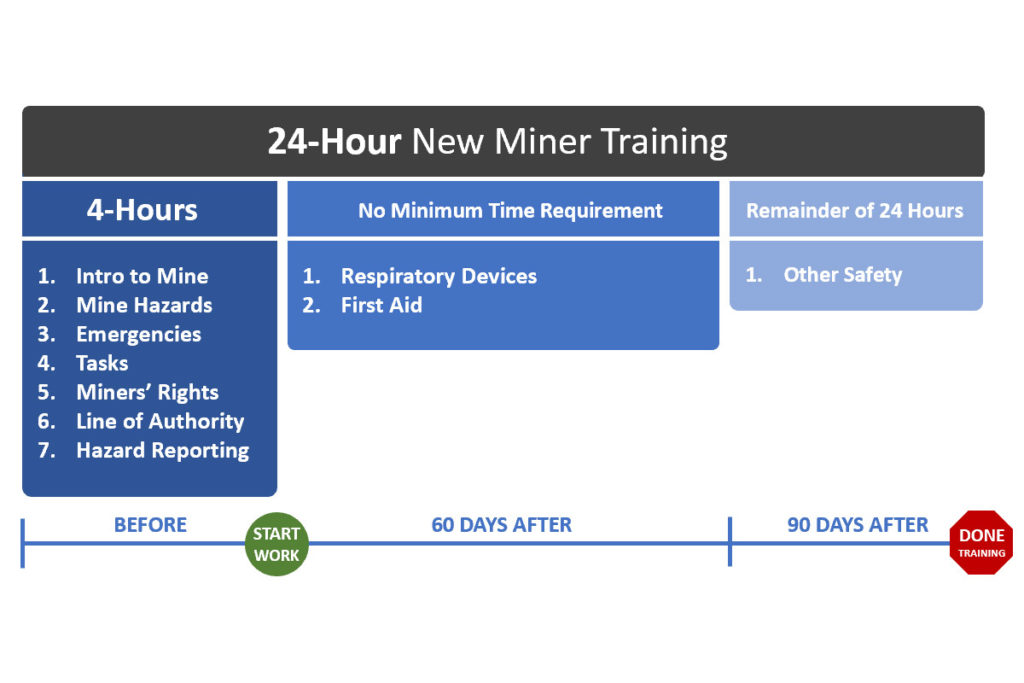
Acceptable training methods include:
- Lecture
- Discussion
- Audio-visual media
- Tour of a facility or site
- Computer-based or online training
An acceptable training method for health and safety aspects of tasks includes “practice under the close observation of a competent person…, if hazard recognition training specific to the assigned task is given before the miner performs the task.”
Recording and certifying the completion of this training on a compliant record of training is required upon completion for all miners.
Newly Hired Experienced Miner
Part 46.6 Newly Hired Experienced Miner Training outlines the requirements for training a newly hired experienced miner.
A newly hired experienced miner is defined as “an experienced miner who is beginning employment with a production-operator or independent contractor. Experienced miners who move from one mine to another, such as drillers and blasters, but who remain employed by the same production-operator or independent contractor are not considered newly hired experienced miners.”
Required training subjects prior to beginning work at the mine include:
- Introduction to the work environment, including a mine tour
- Hazard recognition and avoidance
- Emergency procedures
- Health and safety aspects of tasks
- Statutory rights of miners and miners’ representatives
- Line of authority
- Hazard reporting
Required training subjects within 60 days of beginning work at the mine include:
- Self-rescue and respiratory devices (if used at the mine)
Acceptable training methods include:
- Lecture
- Discussion
- Audio-visual media
- Tour of a facility or site
- Computer-based or online training
An acceptable training method for health and safety aspects of tasks includes “practice under the close observation of a competent person…, if hazard recognition training specific to the assigned task is given before the miner performs the task.”
There is no minimum amount of time required for newly hired experienced miner training, but the specified 7 subjects must be completed BEFORE the miner begins work at the mine, followed by training on respiratory devices within 60 days after beginning work at the mine.
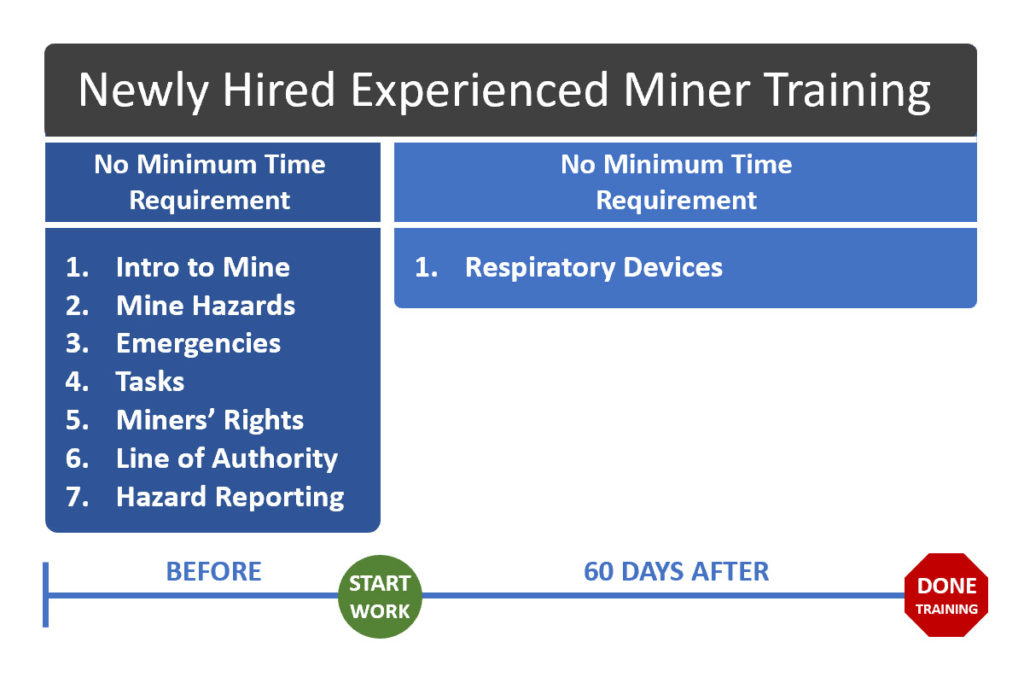
Recording and certifying the completion of this training on a compliant record of training is required upon completion for all miners.
This training is NOT required for an experienced miner “who returns to the same mine, following an absence of 12 months or less… Instead you must provide such miner with training on any changes at the mine that occurred during the miner’s absence that could adversely affect the miner’s health or safety. This training must be given before the miner begins work at the mine. If the miner missed any part of annual refresher training… during the absence, you must provide the miner with the missed training no later than 90 calendar days after the miner begins work at the mine.”
New Task
Part 46.7 New Task Training outlines the requirements for training a new task.
A task is defined as “a work assignment or component of a job that requires specific job knowledge or experience.”
A new task is a task “in which [the miner or mining contractor] has no previous work experience with training in the health and safety aspects of the task to be assigned, including the safe work procedures of such task, information about the physical and health hazards of chemicals in the miner’s work area, the protective measures a miner can take against these hazards, and the contents of the mine’s HazCom program.”
Required training subjects include:
- Health and safety aspects of tasks
- Safe work procedures
- Physical and health hazards of chemicals
- Protective measures to take against hazards
- Contents of mine’s HazCom program

Acceptable training methods include “practice under the close observation of a competent person…, if hazard recognition training specific to the assigned task is given before the miner performs the task.”
There is no minimum amount of time required for site-specific hazard training, but it must be completed BEFORE the miner begins the new task.
Recording and certifying the completion of this training on a compliant record of training is required upon completion for all miners.
New task training is NOT required for “miners who have received training in a similar task or who have previous work experience in the task, and who can demonstrate the necessary skills to perform the task in a safe and healthful manner. To determine whether task training under this section is required, you (the mine operator or mining contractor) must observe that the miner can perform the task in a safe and healthful manner.”
Annual Refresher
Part 46.8 Annual Refresher Training outlines the requirements for annual refresher training.
Annual refresher training “must provide each miner with no less than 8 hours of annual refresher training, no later than 12 months after the miner begins work at the mine… and thereafter, no later than 12 months after the previous annual refresher training was completed.”
This training is required for all miners and mining contractors to remain compliant.
The only required training subject for annual refresher training is “instruction on changes at the mine that could adversely affect the miner’s health or safety.”
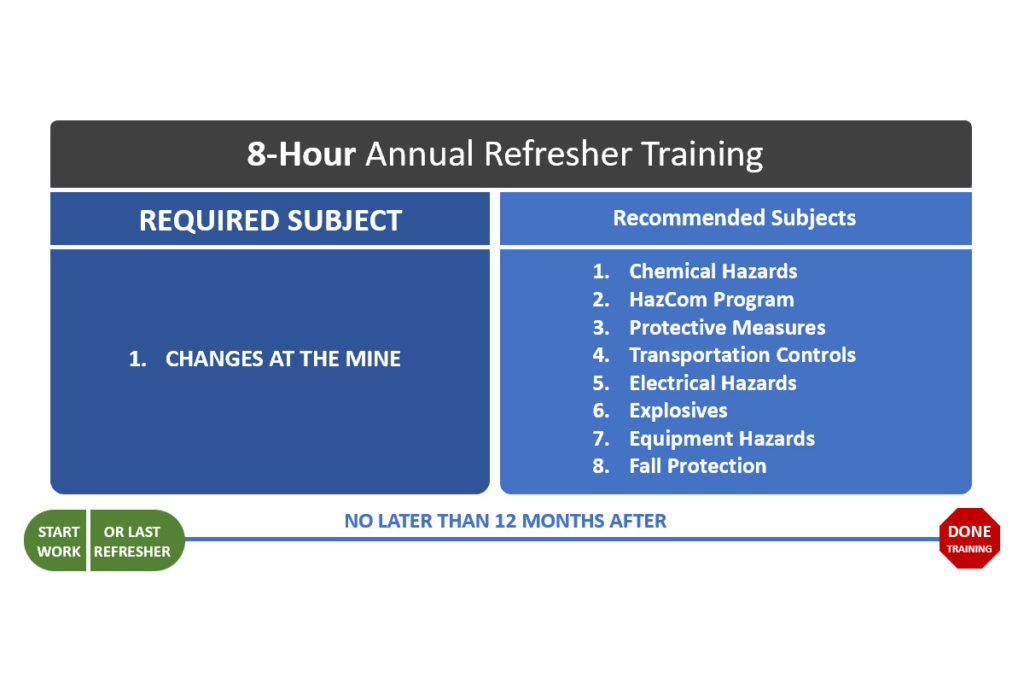
Other subjects recommended by MSHA for annual refresher training include:
- Mandatory health and safety standards
- Information about the physical and health hazards of chemicals in the miner’s work area
- The protective measures a miner can take against these hazards
- The contents of the mine’s HazCom program
- Transportation controls and communication systems
- Escape and emergency evacuation plans
- Firewarning and firefighting
- Ground conditions and control
- Traffic patterns and control
- Working in areas of highwalls
- Water hazards, pits, and spoil banks
- Illumination and night work
- First aid
- Electrical hazards
- Prevention of accidents
- Health
- Explosives
- Respiratory devices
- Equipment Hazards
- Mobile equipment (haulage and service trucks, front-end loaders and tractors)
- Conveyor systems
- Cranes
- Crushers
- Excavators
- Dredges
- Maintenance and repair (use of hand tools and welding equipment)
- Material handling
- Fall prevention and protection
- Working around moving objects (machine guarding)
TIP! – While many mine operators and mining contractors train their teams in a single 8-hour session at the end of the year, MSHA allows for training time to be credited throughout the year. So for example, you could accumulate and credit your team for training time from monthly safety meetings throughout the year and complete your annual refresher training without having to lose an entire 8-hour day of training. That is, of course, as long as you’ve covered “changes at the mine.”
Recording and certifying the completion of this training on a compliant record of training is required upon completion for all miners.
Site-Specific Hazards
Part 46.11 Site-Specific Hazard Awareness Training outlines the requirements for site-specific training.
The site means “an area of the mine where mining operations occur.”
Site-specific hazard awareness training is “information or instructions on the hazards a person could be exposed to while at the mine, as well as applicable emergency procedures. The training must address site-specific health and safety risks, such as unique geologic or environmental conditions, recognition and avoidance of hazards such as electrical and powered-haulage hazards, traffic patterns and control, and restricted areas; and warning and evacuation signals, evacuation and emergency procedures, or other special safety procedures.”
This training must be provided to any person who is exposed to mine hazards. While this training is included in new miner and newly hired experienced miner required subjects, non-miners who must receive this type of training include:
- Office or staff personnel
- Scientific workers
- Delivery workers
- Customers, including commercial over-the-road truck drivers
- Construction workers or employees of independent contractors who are not miners
- Maintenance or service workers who do not work at the mine site for frequent or extended periods
- Vendors or visitors
However, while most mines provide site-specific hazard training to everyone who enters the mine, MSHA does require this training “for any person who is accompanied at all times by an experienced miner who is familiar with hazards specific to the mine site.”
Training subjects must include:
- Site-specific health and safety risks
- Unique geologic or environmental conditions
- Electrical and powered haulage hazards
- Traffic patterns and control
- Restricted areas
- Warnings and evacuation signals
- Evacuation and emergency procedures
- Any other special safety procedures
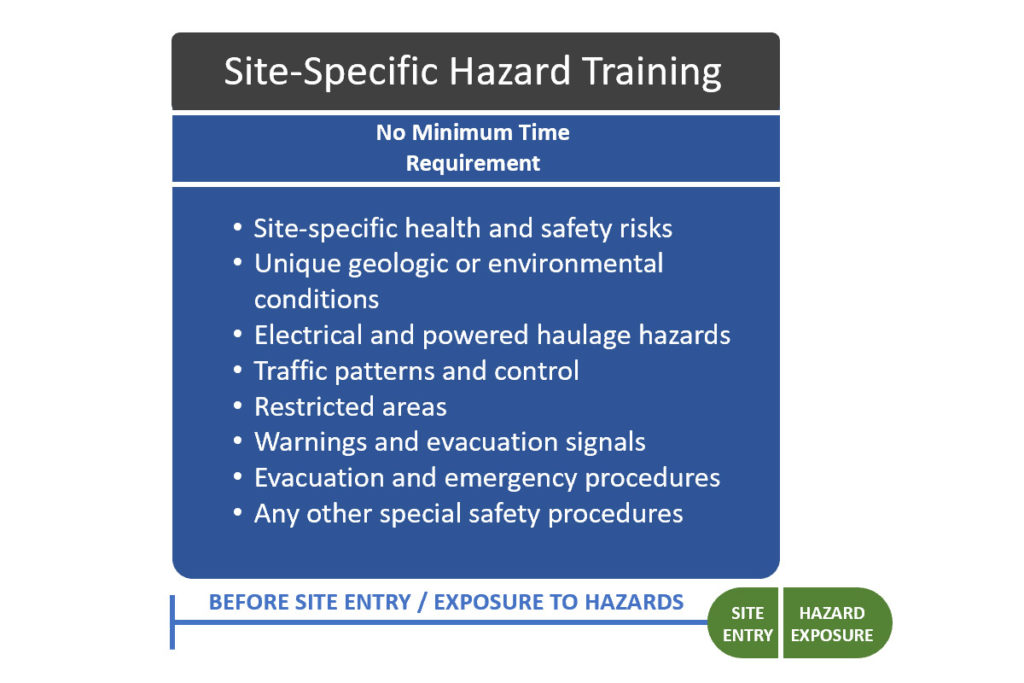
Acceptable training methods include:
- Written hazard warnings
- Oral instruction
- Signs and posted warnings
- Walkaround training
- Other appropriate means that alert a person to site-specific hazards
There is no minimum amount of time required for site-specific hazard training, but it must be completed BEFORE any person is exposed to mine hazards.
Recording and certifying – “You are not required to make records… of site-specific hazard awareness training you provide… to persons who are not miners… However, you must be able to provide evidence to us, upon request, that the training was provided, such as the training materials that are used; copies of written information distributed to persons upon their arrival at the mine; or visitor log books that indicate that training has been provided.”
Compensation For Training
Part 46.10 Compensation for Training states that:
- “(a) Training must be conducted during normal working hours. Persons required to receive training must be paid at a rate of pay that corresponds to the rate of pay they would have received had they been performing their normal work tasks.
- (b) If training is given at a location other than the normal place of work, persons required to receive such training must be compensated for the additional costs, including mileage, meals, and lodging, they may incur in attending such training sessions.”
This requirement is part of what makes Part 46 and Part 48 regulations somewhat different from other federally mandated training. The intent is that the employer provides the training during work hours and pays the miners during such training.
This requires clarification for at least a couple of reasons:
- Many people confuse this type of training for a “certification” that they receive outside of or even before employment at a mine. This isn’t the case. MSHA specifically designed these training requirements to be managed by the mine or mining contractor employer.
- When online training is used as a teaching method, and trainees are taking the training remotely, miners and mining contractors must still be paid for their training time.
Record and Certify Completed Training On A Compliant Part 46 Training Record
Part 46.9 Records of Training outlines the requirements for recording and certifying that training has been completed. MSHA offers Part 46 mine operators and mining contractors 2 options for documentation:
- Use a 5000-23 Certificate of Training form
- Create a compliant record of training that contains required information
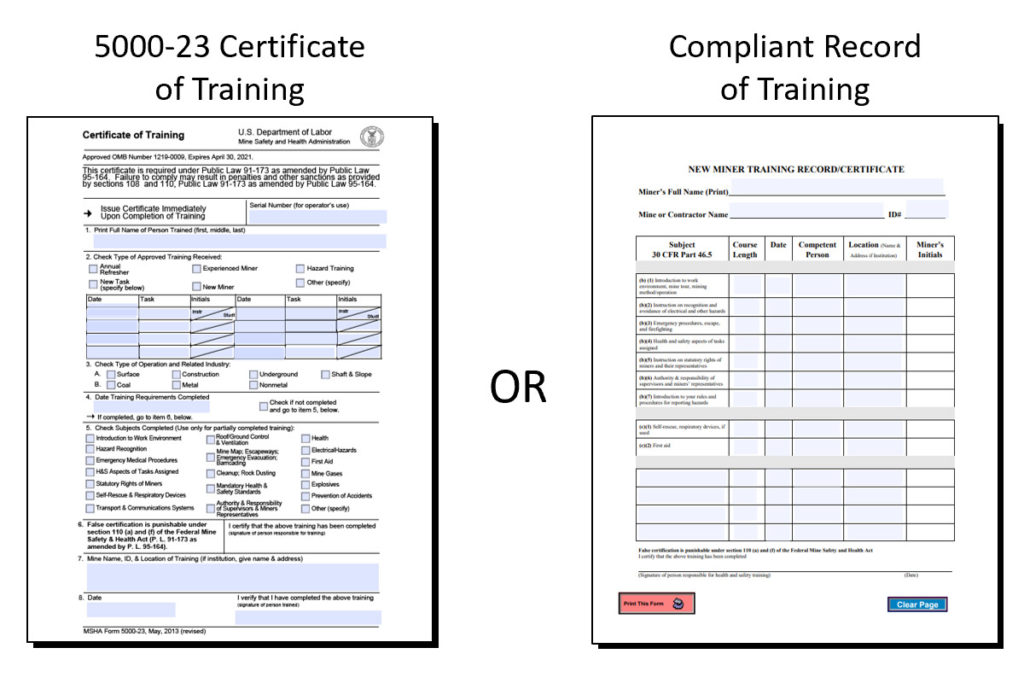
5000-23 Certificate Of Training
If you decide to use a 5000-23 Certificate of Training, you can download the form directly from MSHA’s website, print it out, and fill in the required fields. Keep in mind that this form was originally designed for Part 48 underground miner training. So, it doesn’t directly align with the Part 46 record of training requirements and it’s not very intuitive to fill out.
TIP! – You’ll definitely want to refer to our article, “How To Fill Out A 5000-23 Certificate Of Training” to make sure you complete this form properly.
MSHA-Compliant Record Of Training
If you choose to create your own MSHA-compliant record of training, just include the 5 sets of information required.
(1) The printed full name of the person trained;
(2) The type of training, the duration of the training, the date the training was received, the name of the competent person who provided the training:
(3) The name of the mine or independent contractor, MSHA mine identification number or independent contractor identification number, and location of training (if an institution, the name and address of the institution).
(4) The statement, “False certification is punishable under §110(a) and (f) of the Federal Mine Safety and Health Act,” printed in bold letters and in a conspicuous manner; and
(5) A statement signed by the person designated in the MSHA-approved training plan for the mine as responsible for health and safety training, that states “I certify that the above training has been completed.”
TIP! – For both types of training records, the responsible person who signs and certifies that training has been completed must also be listed and specifically named in your training plan.
When To Record And Certify Training
For a new miner, you’ll complete a record of training no later than:
- when the miner begins work at the mine as required under §46.5(b);
- 60 calendar days after the miner begins work at the mine; and
- 90 calendar days after the miner begins work at the mine, if applicable.
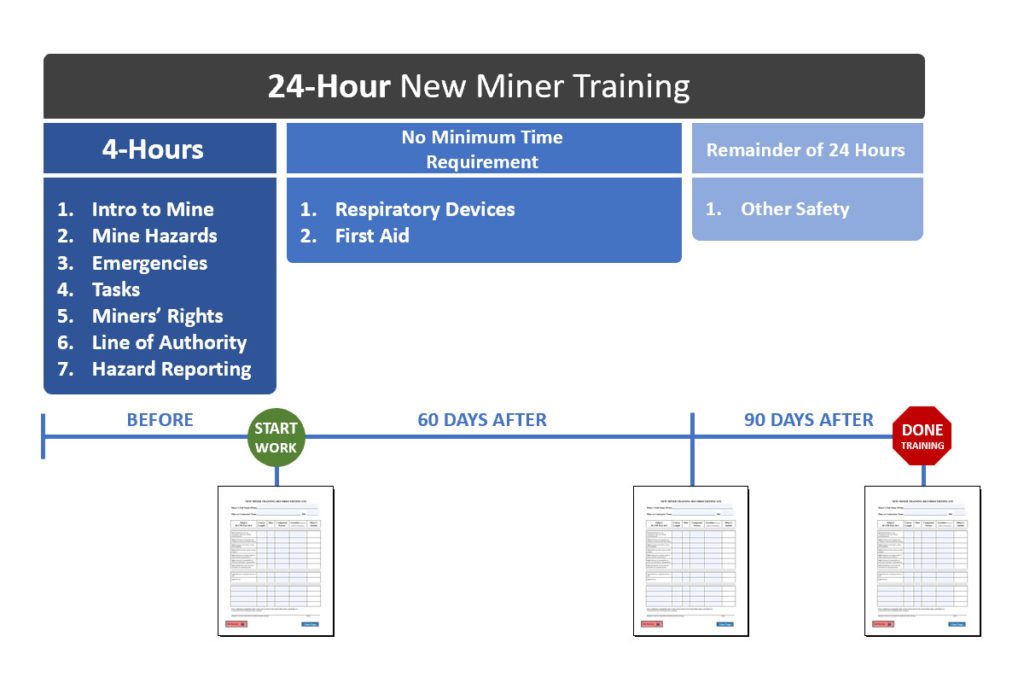
For a newly hired experienced miner, you’ll complete a record of training no later than:
- when the miner begins work at the mine
- 60 calendar days after the miner begins work at the mine

For new task and annual refresher training programs, you’ll complete a record of training upon completion of the training.
For site-specific hazard awareness training, you aren’t required to create a record of training. But you still have to document in some way that the training was provided and completed.
Additional Documentation Requirements
Providing Copies – You must provide miners and mining contractors with copies of their own training records when the miner:
- Complete a required training program
- Terminate employment at the mine
Maintaining Records – You must maintain hard copies and make all training records available for inspection by MSHA, the miners’ representative, and the miner. If not maintained in hard copy, they must be provided upon request.
You must maintain copies of training records during each miner’s employment and for 60 days after termination. However, annual refresher training records are only required to be maintained for 2 years.
Questions?
Got questions? Want to offer some valuable input? See something that needs correction?
Just let us know with a quick message and we’ll get right back to you.